Customer Story
Babcock Marine & Technology
Top 3
in the market sector globally
1891
company founded
28,000
employees
Overview
Babcock’s Marine & Technology (M&T) Division is part of Babcock International Group plc, a multinational corporation which specializes in support services managing complex assets and infrastructure in safety and mission-critical environments. As one of the world’s leading marine support businesses, the Division serves defense and commercial organizations in the UK and beyond. They are the Ministry of Defense’s largest single support services supplier and constantly strive to remain amongst the top three in the market sector globally. To retain their preeminent UK position, grow global business and secure future success, Babcock’s M&T Division drives an aggressive continuous improvement agenda.
Supply Chain Data Optimization
In an increasingly connected business world, data has become a critical currency. A successful business therefore depends on the creation, management, and exploitation of accurate data and information. Data is the foundation on which Babcock’s M&T Division builds customer and supplier relationships, operates processes and manages people. Data that is not fit for business purposes can increase costs, reduce revenues, and increase commercial and regulatory risks, thereby reducing global competitiveness. Customers and partners expect them to manage data on their behalf with care and rigour. Quite simply, the Division sees effective management of data as key to securing future success.
The Supply Chain function is a critical part of Babcock’s M&T Division, managing all aspects of the supply chain. The Division spends over £500 million a year procuring materials and services from over 3,000 suppliers to enable it to service customers and partners. Data on over 1 million commodities and parts needs to be managed. The supply chain poses complex data challenges, and issues were causing inefficiencies and additional costs across the end-to-end process.
The urgency of this challenge was heightened by an enterprise wide process and system redesign; bringing together variable quality data from disparate systems would cause problems when trying to integrate and match it within a single platform.
Industry
Marine technology services
Challenge
- Optimize the data within Babcock Marine & Technology’s supply chain
Results
- 23% increase in supplier master data quality
Solution
“Data is the DNA of our supply chain. Data completeness and accuracy are critical to our current and future operations in an increasingly competitive market.”
Andy Chapell Head of Supply Chain Capability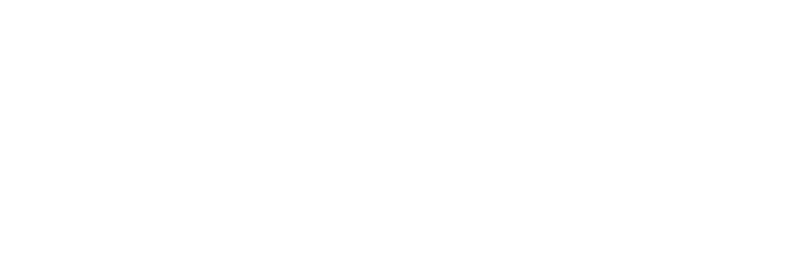
A Strategic Approach to Data Quality
A Strategic Approach to Data Quality The senior managers within the Division’s Supply Chain function put together a strategic plan to address these problems and initiated a five-stage improvement approach to align the organization towards the goal of optimizing the supply chain.
- Babcock’s M&T Division invested heavily over several years in data management best practices and tools:
- The creation of a central data quality team
- A major initiative to identify and capture supplier and product master data
- Assigning clear governance and ownership of key subject areas and data items to named and accountable business owners and data stewards
- The creation of a Divisional Data Dictionary to support governance activities
- Raising data quality awareness amongst senior managers and key operational people
Babcock’s M&T Division recognized the need for a tool to identify and quantify data quality issues, to form the basis of the action plan and serve as a benchmark to measure improvements. They selected the Trillium Discovery data profiling toolset to support their strategic supply chain data objectives.
STAGE 1: Identify critical data subject areas/data elements, and assign owners and stewards
STAGE 2: Define required data standards— both format and content
STAGE 3: Evaluate current data items against the standards, apply rules for monitoring non-compliance and highlight areas for improvement
STAGE 4: Address problems and issues via corrective action plans
STAGE 5: Control via regular data audit reports and dashboards—to monitor improvements and/or any further deteriorations in the data
Ongoing Monitoring and Management of Data Quality
The Trillium Discovery tool is a key component within the Division’s supply chain optimization strategy and enables the Division to understand the quality of their data, develop improvement plans and monitor the data on an ongoing basis.
Trillium Discovery simplified the data profiling and analysis; the sophisticated and unmatched discovery and profiling techniques ensured complete, accurate and reliable assessment of the data. This resulted in better data quality, particularly through the reduction of data inconsistencies and missing and duplicated data. From this, data improvement action plans were developed to discover and fix the root causes, build improvement processes, and monitor and manage the improvements.
The Division now has business people in the Supply Chain function who have been trained to use Trillium Discovery to review failing data rows and export the information so any data inconsistencies can be resolved in their systems.
They have benefited from a 23% increase in supplier master data quality as a result of the optimization project.
Four out of 11 of the Division’s business units have achieved the 98% target for data quality set by the business, with six out of 11 exceeding 95%. The improved recognition of data as a critical asset owned by the business provides multifaceted benefits:
- Identify all Census tracts that contain Bank of America branches and create a map layer to display this information
- Reduced need for rework to overcome data problems, resulting in lower costs and improved process efficiencies
- Better reporting, better analytics and better decision making
- Faster deployment of IT applications to new sites, as the underlying data can be relied on and is therefore more easily migrated
- Enhanced ability of Supply Chain function to demonstrate better regulatory and industry standards compliance
- Reduction in duplicate supplier data entries, enabling better understanding of the totality of supplier relationships and opening the way for more favorable contractual negotiations and terms
Following the success of the supply chain project, Babcock’s M&T Division is now looking to extend these best practice approaches and tools to other business functions, including HR and Finance. As the Division continues to grow, maintaining a sound base of key data will become even more important to securing future success.
Trillium Discovery
Visually assess the quality of your data and support data governance with comprehensive profiling that’s customized to your unique business needs